The surface coating on a screw is just as important as the screwr material itself. Screw threads are created through a cutting or forming machining process, and surface coatings provide an important layer of protection for the screw shank and threads.
To that end, screws benefit greatly from a wide range of engineered surface coatings that are tailored to each screw application in order to provide optimal corrosion and cracking protection.
In a nutshell, surface coatings are applied to screws to increase surface resistance and protect the screw from premature failure due to corrosion or cracking.
So, what are the most common screw treatment methods? The following are the most common screw surface treatment methods:
1. Zinc plating
The most common surface treatment method for Screw is electro galvanizing. It is not only inexpensive, but it also has a lovely appearance. Electroplating is available in black and military green. However, one disadvantage of electro galvanizing is that its anti-corrosion performance is general, and it has the lowest anti-corrosion performance of any plating (coating) layer. In general, the screws after electro galvanizing can pass the neutral salt spray test within 72 hours, and a special sealing agent is also used, so that the salt spray test after electro galvanizing can last for more than 200 hours, but it is more expensive, costing 5-8 times as much as general galvanizing.
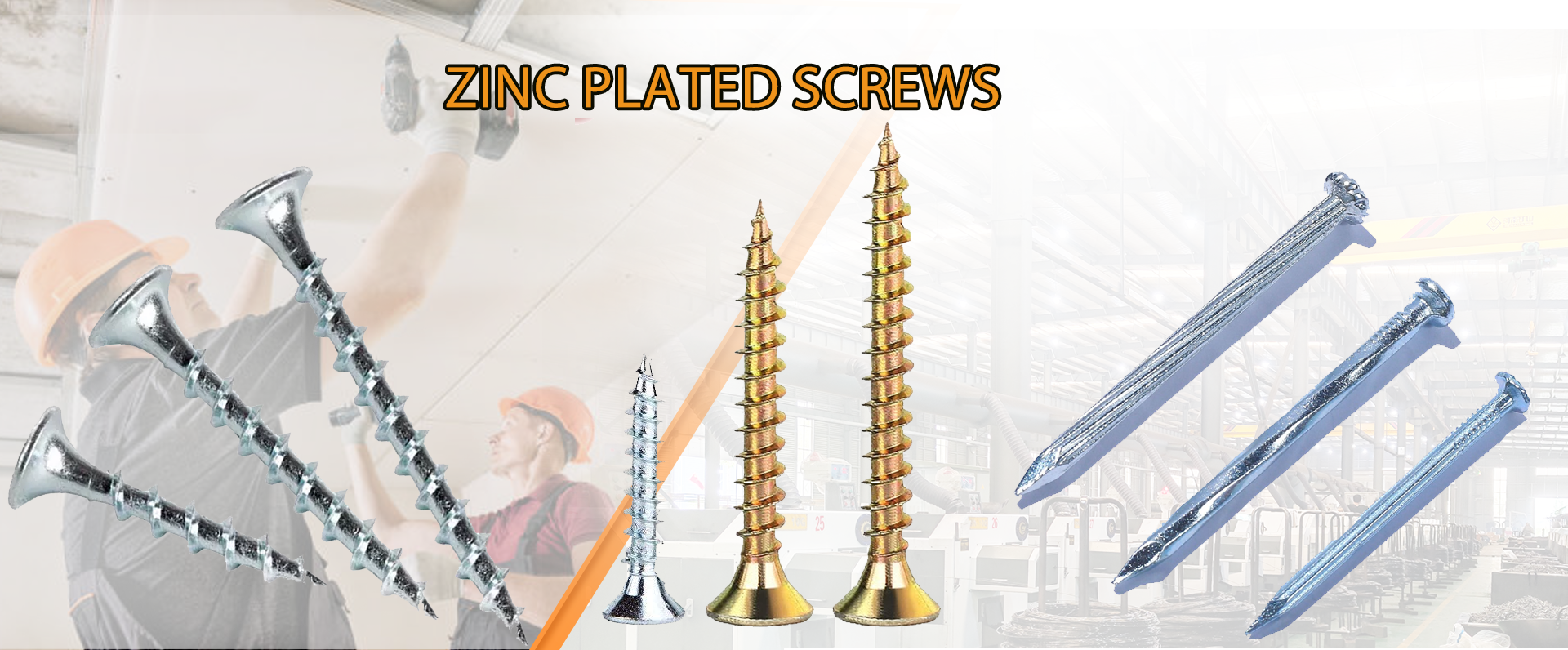
2. Chromium plating
The chromium coating on screw fasteners is stable in the environment, does not easily change color or lose luster, has a high hardness, and is resistant to wear. Although chromium coating is commonly used as a decorative coating on fasteners, it is rarely used in industries requiring high corrosion resistance. Because good chrome plated fasteners are as expensive as stainless steel, they should only be used when the strength of stainless steel is insufficient. To improve chromium plating corrosion resistance, copper and nickel should be plated before chromium plating. Although chromium coating can withstand high temperatures of 1200 degrees Fahrenheit (650 degrees Celsius), it suffers from the same hydrogen embrittlement problem as galvanizing.
3. Silver and nickel plating on the surface
Silver coating for screw fasteners serves as a solid lubricant for fasteners as well as a means of preventing corrosion. Due to the expense, the screws are typically not used, and occasionally the little bolts are also silver plated. Although it tarnishes in the air, silver is still functional at 1600 degrees Fahrenheit. In order to work in high temperature fasteners and prevent screw oxidation, people employ their high temperature resistance and lubricating qualities. Fasteners are typically nickel-plated at locations with high conductivity and corrosion resistance. For instance, the vehicle battery's incoming terminal.
4. Screw surface treatment Dacromet
The surface treatment of Dacromet for screw fasteners does not contain hydrogen embrittlement, and torque preload consistently performs very well. However, it pollutes seriously. Without taking into account the issues with chromium and environmental protection, it is actually most suitable for high strength fasteners with strong anti-corrosion requirements.
5. Surface phosphating
Although phosphorating is less expensive than galvanizing, it offers less protection against corrosion. Screw fasteners should be oiled after phosphating because the oil's performance has a lot to do with the corrosion resistance of the fasteners. Apply general antirust oil after phosphating, and the salt spray test should only take 10 to 20 hours.The screw fastener can take 72–96 hours if advanced antirust oil is applied, but the cost is 2-3 times higher than phosphating oil. Because their torque and pre-tightening force have good consistent performance, the majority of industrial screw fasteners are treated by phosphating + oiling. It is frequently employed in industrial building because it may satisfy the anticipated fastening needs during the assembly of parts and components. Particularly when connecting some crucial components, some screws use phosphating, which can also prevent the issue of hydrogen embrittlement. As a result, in the industrial field, screwwith a grade higher than 10.9 are typically phosphated.
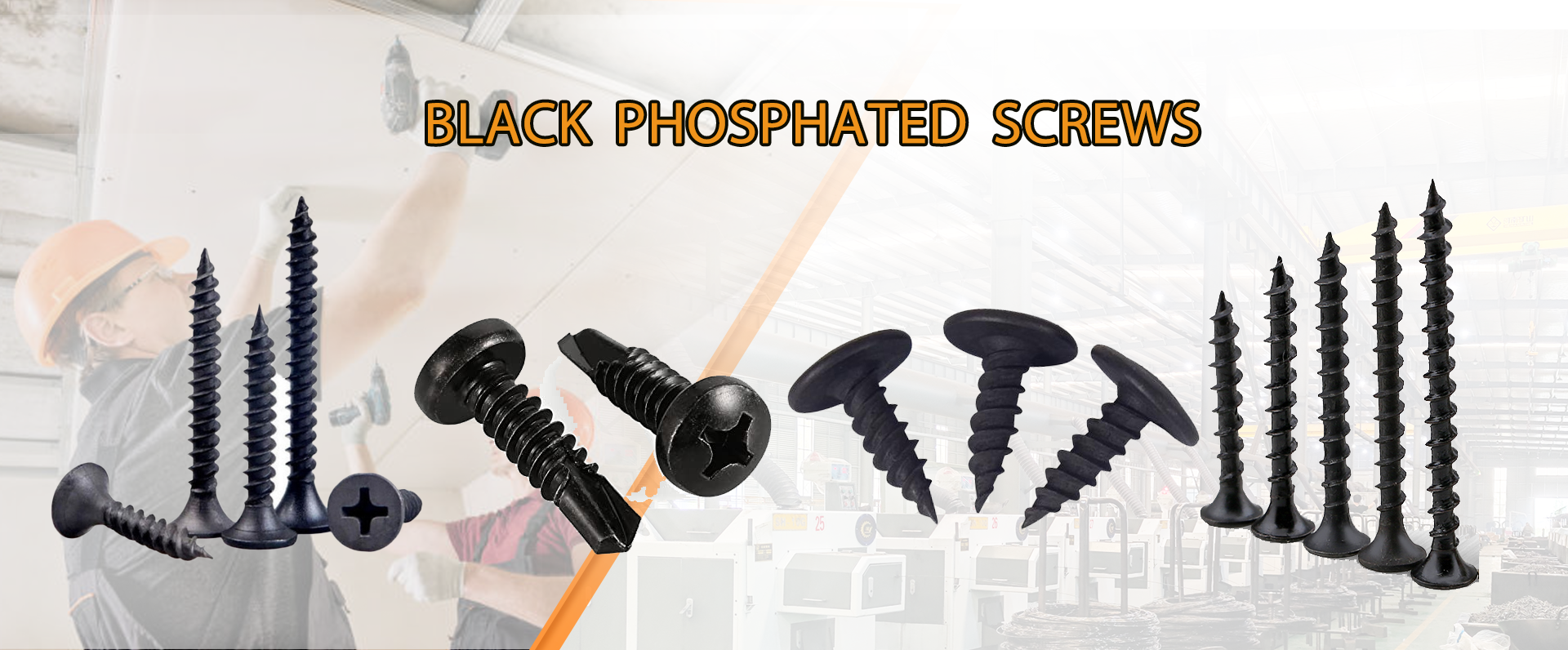
Post time: Feb-15-2023